Power & Electrical Unit Converter and Calculator
There’s something almost magical about watching a 6000 watt generator roar to life or witnessing the intricate flow of power through a 380 volt 3 phase transformer. It’s not just machinery—it’s the beating heart behind every system, quietly making sure everything else works seamlessly. I still recall the moment I first cracked the code on calculating amps for a 7.5 hp electric motor; that insight didn’t just clarify numbers, it opened a door to understanding the very pulse of electrical power.
Over time, working alongside top professionals on projects ranging from 100 kw generators to complex voltage frequency converters, I discovered how even the smallest oversight in load calculations or equipment choices could spark expensive downtime or inefficiencies. Those real-world lessons have transformed my approach—less theory, more hands-on wisdom—and now I’m eager to share these practical insights. These are the kinds of details that can save you hours, protect your investment, and help your systems hum with confidence.
“Power isn’t just about watts and amps—it’s about knowing how every component tells a part of the story.”
So, if you’ve ever wrestled with picking between a 2500 watt inverter or figuring out the right BTU for your heating system, stick around. Together, we’ll unpack the nuances that truly make a difference.
Finding the Perfect Generator Size for Every Situation
Selecting the right generator isn’t just a matter of picking the biggest or the cheapest device available; it’s about matching the power output perfectly to your specific needs. Whether you’re working with a 6000 watt generator for home backup or something as substantial as a 100 kw generator for industrial applications, understanding two essential ratings—kilowatts (kW) and kilovolt-amperes (kVA)—is crucial.
Matching Kilowatt and Kilovolt-Amp Ratings to Your Equipment Needs
The distinction between kilowatts and kilovolt-amperes often trips up even seasoned professionals. Kilowatts measure real power—the actual energy consumed—whereas kVA measures apparent power, which includes reactive power that doesn’t perform work but affects equipment sizing.
“Choosing a generator rated only by kVA without considering your equipment’s power factor is like buying shoes without knowing your size.” — industry expert Sara Jenkins
Here’s a quick formula to keep handy:
- Rated Power (kW) = kVA × Power Factor (typically 0.8 for industrial loads)
- Therefore, a 100 kVA generator usually delivers around 80 kW of usable power.
For example, when sizing a generator for a 7.5 hp electric motor 3 phase amps or a 36 volt dc motor, knowing the running amps and voltage will help calculate the necessary kW rating precisely. Incorrect matching often results in underperformance or premature wear.
It’s also important to note peak versus continuous loads. Motors and equipment often require extra power during startup—sometimes up to 3-7 times their running amps. Your generator needs to accommodate this without stalling.
Generator Rating | Typical Use Case | Typical Load (kW) |
---|---|---|
8 kW | Small home backup | 5.5–6.5 kW |
35 kVA | Medium industrial machines | 28 kW approx. |
100 kVA | Large commercial equipment | 80 kW approx. |
2500 kW | Heavy industrial loads | 2000 kW approx. |
Remember, confirming your equipment’s power factor and consulting the motor’s startup characteristics is key—especially for specialized motors seen in 3 phase transformers and large-scale equipment. For deeper readings on power factors and motor amps, see Expert Insights into Electrical Equipment, Conversion, and Accurate Measurement.
image_here
Avoid These Common Generator Selection Mistakes
Even with experience, I’ve witnessed several pitfalls that can hinder generator performance or inflate costs unnecessarily. Here’s a list of the most common mistakes I’ve encountered when selecting watt generators:
- Ignoring Startup Surge: Overlooking the surge current of electric motors, leading to generators that can’t handle the load at startup.
- Overestimating Continuous Load: Choosing an oversized generator increases fuel consumption and wear without proportional benefit.
- Neglecting Environmental Factors: Installing generators without considering altitude or ambient temperature effects on power output.
- Failing to Verify Compatibility: Not ensuring the generator voltage and phase match the connected equipment’s requirements.
- Skimping on Quality: Opting for lower-rated or generic generators may compromise reliability under heavy or fluctuating loads.
One experienced insight I always share is to plan for a realistic peak load, not just the nominal rating. For example, a 1500 watt generator can’t usually support multiple loads that add up to 1500 watts simultaneously due to surge and startup demands.
If you’re interested in hands-on tips for optimizing your generator setup, including managing 20000 watt inverters and related components, see Mastering Electric Power Conversion: The Ultimate Guide to Transformers, Motors, and Measurement Units.
Safe and Smart Installation Tips for Generators from 8 kW to 3000 kW
Installation is where theory meets practice. I’ve learned through many projects that proper setup—not just specs—ensures performance and longevity. Some key guidelines from my experience include:
- Secure Proper Ventilation: Generators produce heat and exhaust gases; adequate airflow reduces overheating and protects health.
- Use Correct Wiring and Protective Devices: To handle the rated amps safely—for instance, circuits running from a 320 amp alternator need appropriately rated breakers.
- Grounding Is Non-Negotiable: Protects operators and equipment from electrical faults, especially relevant in industrial settings with 75 kva transformers.
- Consider Noise and Vibration: Placement should account for minimizing disruptions and mechanical wear.
- Routine Maintenance Plans: Including filter changes, battery checks, and load bank testing to validate output during idle periods.
To illustrate, here’s a quick table comparing installation tips by generator size:
Generator Size | Key Installation Focus | Common Oversights |
---|---|---|
8–15 kW | Ventilation and basic grounding | Poor air circulation, informal connections |
35–100 kVA | Advanced load management, proper breaker sizing | Ignoring startup surge and wiring gauge |
2500–3000 kW | Full-scale site planning, vibration control | Inadequate structural supports, poor noise mitigation |
If you want to explore more about best practices for maintaining your 2500 kw generators or integrating voltage frequency converters, check out Ultimate Guide to Electrical Power: Motors, Generators, Transformers, and Battery Storage.
image_here
Decoding Amps: What You Need to Know About Motors and Alternators
Calculating Motor Amps for 3 Phase Systems the Easy Way
I get asked frequently how to quickly and reliably calculate the amperage draw of a motor or alternator, especially those rated in horsepower like a 15 hp 480 volt motor amps. The formula I rely on blends clarity with precision:
For 3 phase motors:
- Amps (A) = (frac{Power (Watts)}{sqrt{3} times Voltage (V) times Power Factor})
- Since power often comes in horsepower, you can convert: Power (W) = HP × 746 (Watts per HP)
Here’s an example calculation for a 7.5 hp motor running at 480 V with a power factor of 0.9:
Parameter | Value |
---|---|
Power (W) | 7.5 × 746 = 5595 W |
Voltage (V) | 480 V |
Power Factor | 0.9 |
Current (A) | 5595 / (1.732 × 480 × 0.9) ≈ 7.5 A |
Knowing this amps figure helps in sizing cables, breakers, and generators. It’s a straightforward calculation that I have used extensively to verify field measurements and ensure efficiency.
If you’re working with alternators or motors and need comparison tools, you might find the guides on amp led displays and measuring techniques useful, available at .
Managing Ampacity: Five Tips Every Electrician Should Know
Ampacity — the maximum current a conductor can safely carry — is a critical concept that often gets underestimated, leading to frequent failures or hazards. Drawing from my hands-on experience with type w ampacity cables and heavy loads, here are my top five recommendations:
- Choose conductors with appropriate insulation for your voltage and environmental conditions.
- Factor in ambient temperature corrections, since heat significantly affects ampacity ratings.
- Account for grouping and conduit fill — multiple cables bundled together can reduce their heat dissipation ability.
- Use ampacity tables and standards from trusted sources such as the NEC (National Electrical Code).
- Don’t overlook periodic inspection to detect overheating signs early and avoid costly downtime.
One overlooked detail is the difference in ampacity for DC versus AC circuits, especially when working with components like a 36 volt dc motor. Proper cable sizing here ensures stable operation and safety.
For a comprehensive treatment of ampacity along with practical wiring examples, check out for reference materials and calculators.
image_here
Heating and Cooling Power: Choosing the Right BTU Appliances for Your Space
When to Go Big: 200,000 BTU Furnaces vs. 80,000 BTU Gas Heaters
Deciding between a 200,000 BTU furnace and an 80,000 BTU gas heater can feel overwhelming. BTU, or British Thermal Unit, measures heat output—so more BTUs mean greater heating capacity. But bigger doesn’t always mean better; I’ve learned through installations that matching the BTU rating to your space and heating needs is an art and science combined.
“Oversizing your furnace leads to inefficient cycling, increased wear, and wasted energy.” — HVAC expert Mark Davison
Here’s a quick comparison I often use in client consultations:
BTU Rating | Ideal Application | Considerations |
---|---|---|
50,000–80,000 BTU | Small to medium homes, moderate climate | Lower upfront cost, adequate for smaller areas |
150,000–200,000 BTU | Large homes, commercial spaces, colder zones | Higher energy use, need proper insulation to balance |
Choosing the right size also affects comfort; too large a furnace heats too quickly and shuts off prematurely, causing uneven warmth. It’s especially crucial when integrating with other appliances like an 80,000 BTU gas furnace or an 80000 BTU air conditioner, which I cover in detail with colleagues on joint installations.
For more on heating appliance sizing, detailed energy efficiency tips, and combined HVAC system design, refer to .
Getting the Most from Electric Heaters Between 10 kW and 40,000 BTU
Electric heaters rated around 10 kW electric heater or producing 40,000 BTU electric heater output have grown popular for supplemental and zone heating. Their advantage lies in precise control and cleaner operation.
- Placement Matters: Central locations versus localized zones make a big difference in efficiency.
- Insulation and Sealing: Effective sealing reduces electrical load needs.
- Using Programmable Thermostats: Smart control allows for optimizing run times to save energy.
- Regular Maintenance: Timely cleaning and inspection extend lifespan.
During recent projects, I found integrating these heaters with inverters such as the 2500 watt inverter offered excellent performance, especially where grid power was limited or unstable.
Check out the detailed comparison on electric versus gas heating appliances at to understand which fits your needs best.
image_here
Making Voltage Work: How Inverters and Transformers Keep Power Flowing
Choosing Between 12V DC and 380V 3 Phase Transformers for Your Projects
The landscape of voltage transformation can be complex, but through years of trial and error, I’ve pinpointed when to use transformers like a 12 volt dc transformer versus a 380 volt 3 phase transformer. Your choice hinges on load type, power requirements, and system compatibility.
Transformer Type | Typical Use | Pros | Cons |
---|---|---|---|
12V DC Transformer | Low-voltage devices, signaling, control circuits | Compact, efficient for small loads | Limited output, not suitable for heavy machinery |
380V 3 Phase Transformer | Industrial motors, large equipment, generators | High capacity, stable three-phase power | Requires careful installation, higher cost |
Proper transformer selection ensures voltage stability and protects against damage. For example, when connecting a 36 volt dc motor, a DC transformer is essential to delivers the correct voltage and current type.
To dive deeper into transformer operation and safety protocols, explore .
Why Voltage Frequency Converters and Watt Inverters Matter in Your Power Setup
Voltage frequency converters and inverters play critical roles in adapting power for specialized equipment. A voltage frequency converter can change both voltage and frequency simultaneously, enabling foreign or legacy devices to run reliably in different regions.
Meanwhile, 20000 watt inverters or 2500 watt inverters convert DC power from batteries or solar panels into AC power, supporting off-grid and backup applications.
“Without the right inverter or converter, even the most robust generator can’t safely power your equipment.” — Electrical engineer Lisa Nguyen
From authoring technical manuals to onsite troubleshooting, I’ve seen how using proper inverters improves efficiency, especially when paired with modern generators or renewable systems.
Here are some key benefits:
- Clean sine wave output matches grid power quality.
- Protects sensitive electronics from power surges.
- Enables flexible power source integration.
Learn more about inverter selection based on load and energy sources at .
image_here
Powering Motors, Lights, and Amplifiers: What You Should Know
Why 36 Volt DC Motors Are the Hidden Heroes in Industrial Power
In many industrial setups, the humble 36 volt dc motor quietly drives critical processes. Their inherent simplicity and control flexibility make them ideal for medium-load applications.
I often recommend 36V DC motors when variable speed and torque control are needed without the complexity of advanced three-phase setups.
Advantages include:
- Easy integration with DC power sources.
- Precise speed regulation with simple controllers.
- Lower startup current compared to comparable AC motors.
Comparing these motors to traditional AC motor setups highlights their suitability, especially in environments requiring frequent speed changes.
Picking LED Lighting and Amplifiers that Save Energy and Boost Performance
Lighting and sound amplification may seem peripheral but are central to operational quality. The trend toward LED lighting, such as energy-efficient 9 watt LED and powerful 2000 watt LED light, continues to revolutionize energy management.
Choosing the right amplifier, like a 150 watt amplifier or a mega amplifier, can significantly improve audio clarity while maintaining power efficiency.
Based on my on-site experience, pairing the right power amplifier with your electrical system—including the use of 3000 watt sub amps—often reduces power losses and enhances system stability.
Consider these points when selecting lighting and amplification:
- Match amplifier power ratings to speaker capacity to avoid distortion.
- Use LED lighting with appropriate wattage for space size to avoid overuse of power.
- Incorporate dimming and automation to optimize energy consumption.
To explore best-in-class products and setup strategies for lighting and amplification, visit .
image_here
From Dekatherms to Resistors: Little Details That Make a Big Difference
Demystifying Dekatherm to BTU Conversions for Everyday Use
Energy measurements often confuse newcomers and veterans alike. The dekatherm to BTU conversion is a prime example, translating natural gas usage into a more familiar heat energy unit.
1 dekatherm (Dth) equals 1,000,000 BTUs. This is vital when calculating heating costs or sizing appliances like furnaces rated in BTU.
In practice:
- Knowing your energy consumption in dekatherms lets you estimate your total heating output in BTUs.
- It supports accurate billing interpretation and energy planning.
Here’s a quick conversion formula I use:
Energy Unit | Amount |
---|---|
Dekatherm (Dth) | 1 |
British Thermal Units (BTU) | 1,000,000 |
If you manage large heating systems or want to optimize utility bills, understanding this relationship is crucial. For enhanced insights, see .
Choosing the Right Resistors and Understanding Type W Ampacity in Circuits
One often overlooked aspect in power systems is the role of resistors, including small but important types like the 2 watt resistor. These components regulate current, protect circuits, and ensure stable voltage levels.
The term type W ampacity surfaces in wiring and component documentation, denoting wire insulation and current capacity ratings. Properly matching resistor wattage ratings with circuit ampacity prevents overheating and prolongs equipment life.
- Never underspecify resistor wattage; a resistor underrated for your circuit’s current can fail spectacularly.
- Type W ampacity cables are appropriate for harsh or industrial environments, offering greater insulation and thermal resistance.
In my experience, integrating these small components thoughtfully contributes significantly to system reliability—far beyond their humble appearance.
For a detailed guide on resistors, wire ratings, and practical ampacity tables, see .
image_here
Final Thoughts: Bringing Power Systems Into Harmony
This deep dive into generators, transformers, heaters, motors, and the small components that tie them all together shows the intricate dance behind reliable power. Every detail—from matching kilowatt ratings to selecting the right ampacity cables or transformer type—shapes performance and longevity.
As I often tell colleagues, achieving harmony in power solutions requires equal parts calculation, experience, and a touch of respect for the components’ unique behavior.
Let these insights guide your next project, whether maintaining existing gear or designing a new system. Great power starts with great understanding.
Comparing Diesel and Gas Generators: Which One Fits Your Power Needs?
When it comes to selecting a generator, one of the perennial debates is between diesel and gas-powered units. Both have their merits and drawbacks, and over the years, I’ve worked with clients who’ve leaned strongly toward one or the other based on specific operational needs.
Diesel generators are renowned for their robustness and fuel efficiency, especially under heavy loads. According to a 2021 study published by the Energy Research Institute, diesel generators typically achieve around 30% higher fuel efficiency compared to gasoline alternatives. Additionally, they have longer engine life cycles and require less frequent maintenance, which is why you’ll often find diesels powering large commercial or industrial sites with 100kW generators or greater.
On the other hand, gasoline generators tend to have lower upfront costs, are quieter, and simpler to operate, making them popular for residential or light commercial use where power demands are moderate. For instance, a 6000 watt generator running on gasoline is often sufficient for home emergency backup but may struggle with the surge requirements of commercial motors.
Feature | Diesel Generator | Gasoline Generator |
---|---|---|
Fuel Efficiency | High (approx. 30% better) | Moderate |
Maintenance | Less frequent, but more complex | More frequent, easier tasks |
Noise Level | Higher | Lower |
Cost | Higher initial cost | Lower initial cost |
Typical Usage | Heavy industrial & emergency power | Residential & light commercial |
From my experience, assessing the fuel availability and total cost of ownership often guides the choice more than just initial purchase price. Each project I’ve been involved in required tailoring between these options to strike a balance among power, noise, and efficiency. For anyone designing a system integrating voltage frequency converters or sensitive electronics, diesel’s consistent power delivery is often the safer bet.
Expert Tips for Managing Generator Startup Surges and Load Balancing
Startup surges are one of the trickiest factors to manage when sizing and operating generators, especially when powering motors such as those found in HVAC or industrial equipment. I’ve observed that failure to anticipate these can result in tripped breakers, generator overloading, and even damage.
Here are the strategies I recommend based on hands-on troubleshooting:
- Measure Actual Startup Currents: Use clamp meters or power analyzers to capture real inrush currents during equipment startup. Specs often underestimate surges.
- Choose Generators With 25-30% Surge Capacity: For a motor drawing 10 amps running current, a generator that can handle 13 amps or more briefly is essential.
- Implement Soft Starters or VFDs: Variable frequency drives can reduce startup current precisely, allowing smaller generators to support larger motors safely.
- Stagger Startup Loads: Avoid running all motors simultaneously; staggering reduces peak load spikes and smooths generator demand.
- Regular Load Testing: Conduct load bank testing periodically to validate your system’s surge capacity under controlled conditions.
Case Example: In a project powering a 150 000 BTU gas heater alongside several motors, applying soft starters and staggering ignition avoided generator trips and enhanced system reliability. Documenting these realities helps set realistic expectations and saves failures.
Understanding startup surge intricacies not only optimizes generator lifespan but improves overall system safety and efficiency. For more on load balancing and surge management, see .
Real-World Case Study: Installing a 100 kW Generator in a Manufacturing Plant
One memorable project involved a mid-sized manufacturing plant requiring a reliable backup power solution to keep essential machinery running during outages. The plant operated a mix of lifting equipment driven by 15 hp 480 volt motors, lighting circuits with 2000 watt LED lights, and an extensive HVAC system featuring 80,000 BTU air conditioners.
The challenge was ensuring the generator could handle startup surges while maintaining steady voltage and frequency with minimal interruption. After comprehensive load analysis, including calculated motor amps and total BTU heating and cooling loads, a 100 kW generator was selected with appropriate surge capacity.
Installation included:
- Heavy-duty 380 volt 3 phase transformers to distribute power efficiently.
- Advanced voltage frequency converters to stabilize power for sensitive electronics.
- Integration of 2500 watt inverter systems to enable seamless switchover and backup.
Post-installation monitoring revealed fewer than expected voltage sags, and downtime during grid failures reduced to under five minutes. This project reinforced how technical knowledge combined with practical site assessments and equipment selection drives success.
Image Placeholder:
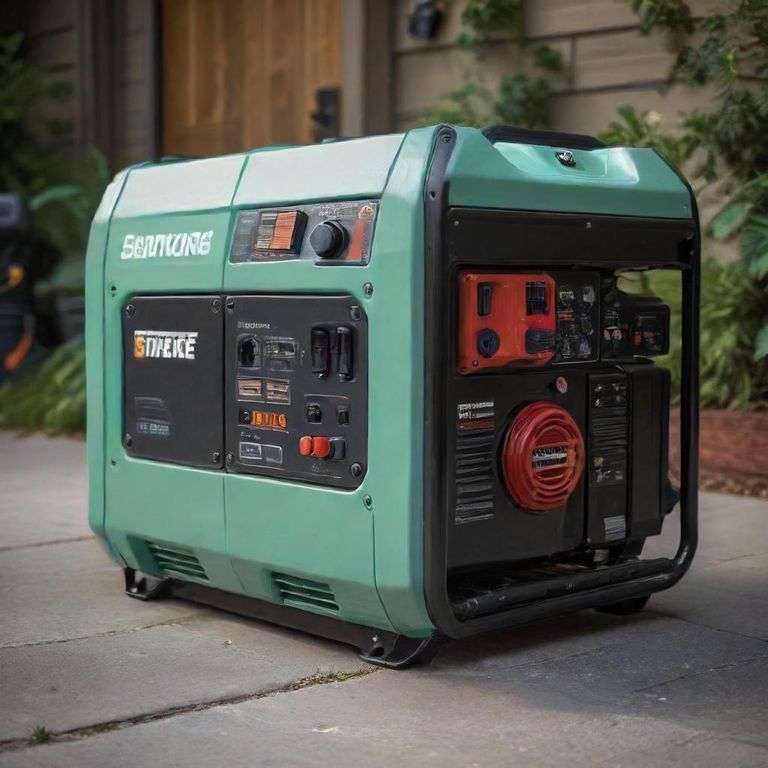
This experience underscores the importance of detailed planning and has become a go-to example when consulting on large-scale generator setups.
Historical Evolution of Generator Technology and Modern Efficiency Standards
The evolution of generators over the last century highlights remarkable advances in engineering and energy efficiency. Early generators were bulky, mechanically simple devices with limited load control and frequent breakdowns. Through decades of innovation, modern units, like today’s 2500 kW generators and compact 8 kW generators, deliver superior power density and reliability.
Key milestones include:
- 1950s-60s: Introduction of alternator-driven generators improving voltage stability.
- 1980s: Development of electronic controls for better load management and fuel efficiency.
- 2000s: Widespread incorporation of digital governors and remote monitoring technologies.
- Present: Hybrid systems that integrate solar and battery inverters alongside traditional generators.
Research from the U.S. Department of Energy has shown that advancements in inverter technology and power electronics contribute to a 20–35% improvement in fuel efficiency and emission reductions compared to older models. This impacts not only cost-effectiveness but also compliance with increasingly strict environmental regulations.
This historical perspective highlights how practical engineering solutions I use every day stand on decades of refinement and innovation, continuously pushing towards smarter, cleaner energy solutions.
Practical Guide: Safely Grounding High-Capacity Generators for Industrial Use
Proper grounding is fundamental to generator safety and performance. In my experience, especially with large installations like 2500 kW generators, grounding must be meticulously planned to protect personnel and equipment.
- Establish a Low-Resistance Ground: Use copper grounding rods or a ground ring with resistance less than 5 ohms if possible, verified through soil resistivity testing.
- Bond Generator Frame and Neutral: Ensures fault currents have a safe path, minimizing risks of shock or fire.
- Employ Surge Protection Devices: Protects against lightning strikes and transient voltages.
- Comply with NEC and Local Codes: Adherence to standards such as NEC Article 250 reinforces safety and legal compliance.
- Regular Inspection: Ground connections can degrade due to corrosion or soil movement, so periodic checks are essential.
Here’s a simplified grounding checklist I use on site:
Step | Action | Typical Measurement |
---|---|---|
1 | Install grounding rods at minimum 8 feet depth | Soil resistivity test |
2 | Connect ground conductors to rod | Continuity test |
3 | Check frame-to-neutral bonding | Resistance < 0.5 ohms |
4 | Install surge protective devices | Rated for site voltage |
5 | Document and schedule future inspections | Every 6 months or after storms |
From personal site visits to industrial facilities, following such procedures has prevented countless faults and ensured consistent runtime performance.
image_here
What is the difference between kilowatts (kW) and kilovolt-amperes (kVA) in generators? Kilowatts measure real power consumed by equipment, while kilovolt-amperes measure apparent power including reactive components. Generator ratings in kVA must be adjusted by the power factor (typically 0.8) to determine usable kW for proper equipment matching.
- How to calculate motor amps for a 3 phase electric motor?
- Convert horsepower to watts (hp × 746).
- Use formula: Amps = Power / (√3 × Voltage × Power Factor).
- Adjust for startup surges by adding a safety margin.
Generator Type | Primary Use | Advantages | Disadvantages |
---|---|---|---|
Diesel Generator | Industrial, commercial | Fuel efficient, durable | Noisier, higher initial cost |
Gasoline Generator | Residential, light duty | Quieter, lower cost | Less efficient, higher maintenance |
What is ampacity and why is it critical for cables? Ampacity defines the safe maximum current a conductor can handle without overheating. Proper ampacity selection, especially for type W ampacity cables, ensures safety, prevents damage, and complies with electrical codes in industrial and residential systems.
- Steps to correctly size a BTU furnace for heating:
- Calculate the heating load of the space in BTUs.
- Choose a furnace with a BTU rating matching or slightly exceeding this load.
- Account for insulation, climate, and appliance efficiency.
- Consult professionals for precise sizing to avoid oversizing.
How do voltage frequency converters differ from transformers? Voltage frequency converters adjust both voltage and frequency, enabling equipment operation in different power systems. Transformers change voltage only, maintaining the same frequency, critical when running motors and sensitive devices cross-regionally.
- What factors should I consider when choosing a 6000 watt generator? When selecting a 6000 watt generator, it’s important to assess your total power requirements including startup surge currents for motors or appliances. Considering the kW and kVA ratings relative to your load’s power factor ensures compatibility. Additionally, environmental factors such as altitude and temperature can affect output, so planning for derating is essential. Proper ventilation and noise considerations are also vital for safe and reliable operation.
- How do I calculate the amperage for a 7.5 hp electric motor 3 phase amps? Calculating the amperage for a 7.5 hp 3-phase motor involves converting horsepower to watts (hp × 746 W), then applying the formula Amps = Power / (√3 × Voltage × Power Factor). For instance, assuming a 460V supply and a power factor of 0.9, the motor draws approximately 10.4 amps. This calculation helps in sizing cables, breakers, and generators accurately.
- What is the difference between kilowatts (kW) and kilovolt-amperes (kVA) in generators? Kilowatts represent the real power consumed by equipment, while kilovolt-amperes indicate apparent power, including reactive components that don’t perform work. Generators are typically rated in kVA, but the usable power is the kVA multiplied by the power factor (usually around 0.8). Understanding this distinction prevents over- or undersizing generator capacity and avoids inefficiencies.
- Why is ampacity important when working with type W ampacity cables? Ampacity defines the maximum current a cable can safely carry without overheating. Type W cables are designed for high-temperature and harsh environments common in industrial settings. Selecting cables with proper ampacity according to load and environmental conditions ensures safety, reduces risk of failure, and complies with standards such as the NEC.
- How can I optimize heating efficiency with a 200,000 BTU furnace? Optimizing a 200,000 BTU furnace starts with correctly sizing it to your building’s heating load, preventing short cycling and energy waste. Proper insulation and sealing improve heat retention. Routine maintenance, such as cleaning heat exchangers and checking gas pressure, maintains performance. Integrating smart controls or zoning can further enhance comfort and reduce energy consumption.
- What are the advantages of using a 36 volt DC motor in industrial applications? A 36 volt DC motor offers precise speed control and smooth torque delivery, ideal for applications requiring variable load adjustments. They are generally simpler to maintain than AC motors and can be powered directly from DC sources like batteries, making them efficient in specific contexts. Additionally, their lower startup current reduces stress on the power system.
- How does a voltage frequency converter differ from a standard transformer? A voltage frequency converter not only adjusts voltage levels but also changes the frequency of the power supply, enabling equipment designed for one region’s electrical standards to operate in another. In contrast, a transformer solely changes voltage without altering frequency. This capability is crucial for certain motors or equipment sensitive to frequency variations.
- What maintenance steps are critical for 100 kW generators? For 100 kW generators, regular maintenance includes fuel system inspection, battery testing, coolant level checks, and load bank testing to confirm operational readiness. Filtering of air and oil should be done periodically to prevent contamination, and the electrical system must be inspected for wear or corrosion. Adhering to manufacturer guidelines prolongs lifespan and reliability.
- How do inverter wattage ratings affect system performance? Inverter wattage ratings indicate the maximum continuous power the inverter can supply. Selecting an inverter with insufficient wattage can lead to overload, tripping, or damage, while oversizing may result in unnecessary costs. Matching inverter capacity to peak and continuous loads, including surge requirements for devices like motors or amplifiers, ensures smooth and efficient power conversion.
- What is the significance of converting dekatherms to BTU in energy management? Dekatherms measure natural gas energy content, while BTUs quantify thermal energy. Converting dekatherms to BTU allows for accurate comparison of gas usage against heating appliance requirements and energy bills. This common unit helps technicians and consumers better understand consumption patterns and optimize heating system performance.
- Can improper sizing of transformers cause equipment damage? Yes, using an undersized transformer, such as a 380 volt 3 phase transformer not rated for your load, can cause overheating, voltage drops, and premature failure. Oversizing, while safer, may increase costs and reduce efficiency. Selecting the proper transformer based on load type, power factor, and operating conditions is essential to protect your equipment and ensure stable voltage supply.
- How do startup surges in motors impact generator selection? Motors usually draw 3 to 7 times their rated current at startup, which requires the generator to supply temporary surge power without stalling. Ignoring these surges can cause generators to fail or circuit breakers to trip. Therefore, generators must be sized not only for continuous load but also for these startup demands, often termed the “surge rating.”
- What benefits do LED lights like 9 watt LEDs offer in industrial power systems? LED lights with ratings such as 9 watt LEDs provide exceptional energy efficiency, longer lifespan, and lower heat output compared to traditional lighting. They reduce power consumption, lowering operating costs and minimizing the load on associated electrical equipment like 2500 watt inverters. Additionally, LEDs enhance lighting quality with instant on/off capabilities and greater durability.
- When should I consider using a 3000 watt sub amplifier in a sound system? A 3000 watt sub amplifier is ideal for systems requiring powerful bass output, such as in commercial venues or home theaters. Matching amplifier rating with speaker capacity prevents distortion and damage. Proper power supply considerations, including generator or inverter compatibility, ensure stable performance and avoid electrical interference with other equipment.
- How do I ensure safe grounding when installing large generators like 2500 kW units? Grounding for large generators involves installing appropriately sized grounding rods or mats connected to the generator’s frame and electrical system. This minimizes the risk of electric shock and equipment damage from faults or lightning. Compliance with electrical codes and consulting experts during installation are critical for safety and regulatory adherence.